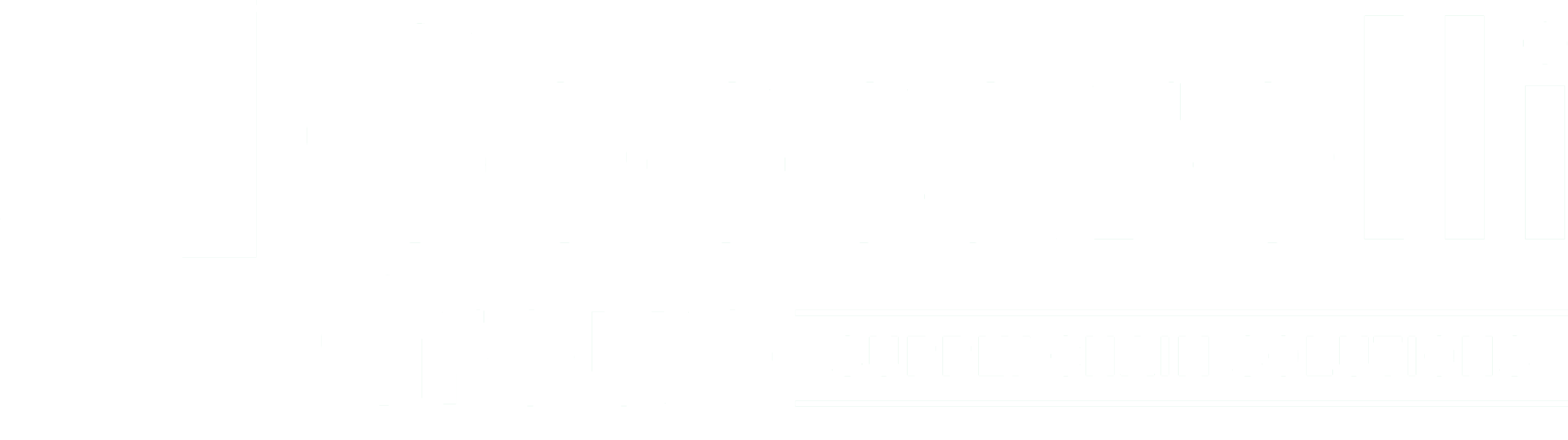
Il Magazzino del Mese of Biofarma Group : Logistics in perfect shape
Biofarma Group is synonymous with health and body care but also with a logistics made up of tense flows and continuous optimizations thanks (also) to the collaboration with the reference logistics operator (Ceccarelli Group). Here's how it works.
There are major transformations that take place, first of all, under the logistical epidermis of companies and thus spread new life throughout the organization. The recent history of Biofarma Group contains a chapter of this type. About two years ago, the Friulian company, together with its historical partner Ceccarelli Group, started a process of reviewing its internal flows to optimize production and distribution processes and increase efficiency and flexibility. The project has not only revolutionized internal logistics, but also injected new organizational logics into the company.
Biofarma is a relatively young name in the Italian pharmaceutical scene. The Mereto di Tomba (Udine) company was born in 1987 from a spin-off of Dipharma, a pharmaceutical company in which Germano Scarpa, founder and CEO of Biofarma, was then responsible for nutraceutical production. The company took its first steps in the production of private label cosmetics and then, in the mid-90s, expanded its range to also include food supplements. Today Biofarma produces and packages, exclusively for third parties, not only cosmetics and supplements but also medical devices for oral and topical administration, as well as probiotic-based drugs. The service offered is complete and transversal: from the development of customized solutions to the creation and production of the finished product.
Innovation has therefore always been part of its genetic heritage. Born as a small start-up, Biofarma is now a reality that operates in over forty countries. Since 2017 it also has a foot in New Jersey (USA) with Biofarma US, a manufacturing and packaging subsidiary specializing in high quality probiotics and nutraceuticals. In February 2020, the merger between Biofarma and Nutrilinea gave birth to Biofarma Group, an industrial reality that includes three other companies in the sector (Apharm, Claire and Pharcoterm). The group now has four production sites in Friuli Venezia Giulia, Lombardy and Veneto (Mereto di Tomba, Cusano Milanino, Gallarate and San Pietro Viminario) - and more than 650 collaborators.
Logistics: a fundamental piece
For a company like Biofarma, which has always been launched towards international growth and expansion, logistics is a fundamental element. This is especially true in times, such as the current ones, in which the challenge is to cope with new distribution models, reduced lead times, flexibility and continuous innovation.
About two years ago, Biofarma therefore decided to put a hand to its production and logistics flows to implement a rationalization and optimization of processes and thus be even more competitive. The warehouse, separated for years and about 35 kilometers from the headquarters and therefore from the production plant in Mereto di Tomba, was decommissioned at the end of 2018. The entire activity was transferred to the new "Biofarma 2" logistics center, built just a few meters from the production plant called “Biofarma 1”, adjacent to the company's headquarters.
The two structures have been conceived to have complementary functions. In addition to the production lines, Biofarma 1 hosts the stocks of raw materials at controlled temperatures (+ 8 ° / + 25 °) for a total of 2,800 pallet places, the semi-finished products at + 15 ° / + 25 ° (2,100 pallets ) and packaging for food supplements (4,000 pallet places). There are also two cold rooms: one + 2 ° / + 8 ° with 150 pallet places and one -22 ° / -18 ° with capacity up to 30 pallet places.
The core of the group's logistics, however, is Biofarma 2: within its approximately 12,000 square meters covered - for a capacity of 19,950 pallet spaces - most of the packaging materials and all finished products subject to different storage conditions are stored. .
Ceccarelli Group's role:
"At the beginning of 2019, the top management of the company asked us for support in the transfer and then in the management of the finished product within the new logistics center," says Matteo Pegoraro, supply chain manager of Ceccarelli Group. The company (see box) boasts a ten-year relationship with Biofarma. “We started by offering transport services - says Pegoraro. - Starting from 2018 we have also been entrusted with the task of managing the handling within their warehouse ".
The date is not accidental. In fact, in 2018, Loglab (acronym for “LOGistics LABoratory”) was born, the fifth company of the Ceccarelli group as well as a business division that provides outsourcing services. “Transport remains in the DNA of Ceccarelli Group but logistics is a natural extension of it - indicates the supply chain manager of Ceccarelli Group. - More and more customers are looking for a provider capable of being not only a supplier of products or services, but rather a single point of contact for all supply chain needs: from storage to distribution ”. And Biofarma is no exception: "In the summer of 2019, the customer asked us for a lean analysis of warehouse flows".
The LogLab approach
The LogLab approach is engineering: analysis and mapping of macro and micro processes, measurement of times and methods, definition of areas for improvement, development and application of new ideas and solutions to overcome any gaps, process monitoring and productivity analysis .
“Abbiamo puntato all’ottimizzazione ridisegnando i flussi ma anche implementando strumenti informatici, sviluppati direttamente dalla nostra software house interna”. Tra questi ultimi, spicca LogLMS (Logistic Management System), un workflow warehouse management system che permette di gestire attraverso un unico software il livello di servizio dell’impianto in termini di procedure operative, sicurezza e così via, ma anche le competenze di ogni operatore (skills matrix as-is e to-be), l’organizzazione dei turni all’interno del magazzino (integrata con le skills matrix), il monitoraggio della produttività per plant, area e operatore.
Reduce waste, optimize processes
The use of LogLMS facilitates the identification of areas where there are non-value-added activities and waste to be reduced or, if possible, eliminated through, for example, the modification of some processes, a different distribution of workloads among the individual operators and so on. “LogLMS is also a staff management tool - summarizes Pegoraro: - it allows to have data in real time so as to be able to intervene where necessary”. The system analyzes the productivity of the entire plant (OPE - Overall Plant Effectiveness), of a single area (OAE - Overall Area Effectiveness) and of the individual warehouse operators (OLE - Overall Labor Effectiveness), helping to identify specific operational or training needs and supporting the company in its choices: “by crossing the KPIs it is possible to define weekly interventions to improve productivity”, confirms Pegoraro.
The intervention of the Ceccarelli Group also led to the re-engineering of processes that Biofarma then chose to entrust completely to its reference partner. "The customer has decided to outsource all the logistics activities carried out within Biofarma 2 and the enslavement of the production lines in Biofarma 1", explains the supply chain manager of Ceccarelli Group. Since 2020, LogLab manages the operational logistics activities within the plant through Lognet, a business network created by Loglab together with the Friul Clean cooperative from Friuli. "On the one hand, the Ceccarelli Group offers engineering design for the simplification of the customer's supply chains and development of information systems for the optimization and monitoring of processes - explains Pegoraro. - On the other hand, Friul Clean intervenes with the implementation of human resources based on the flow of demand. "
About a year after the start of the Ceccarelli business for Biofarma, satisfaction on both sides is declared. The organization of the warehouse and the implementation of tools such as LogLMS have made it possible to obtain advantages in two directions. “We are more flexible in managing peaks - explains Igor Conte, supply chain manager of Biofarma Group. - This is also thanks to the possibility of promptly reorganizing work shifts according to different needs. In general, LMS supports us in the analysis and therefore in the optimization of processes. However, we also have benefits in terms of productivity and efficiency - he continues: - fewer errors, more punctuality. From January to December 2020, we had an overall saving of 30% for the same number of pallets handled ".
All this paves the way for new developments already planned for 2021, such as the installation of Andon monitors, that is, screens that report daily operating levels in real time. The goal is to increase the involvement of warehouse operators and activate a reward system. The adoption of an electronic recall system for the enslavement of production lines, the so-called e-kanban, is also being considered, which would allow to dematerialize the current procedures for material requests by the operating staff, thus reducing paper, time and possibility of errors. and making the process simpler and more immediate.
Last but not least, Biofarma Group is also evaluating the purchase of LGV (Laser Guided Vehicle) vehicles, that is automatic vehicles without a man on board, to be used for the distribution of packaging material in the packaging departments. "Working with a provider like Ceccarelli facilitates the attitude to change and facilitates its implementation - says Igor Conte. - Having a high-level logistics partner at your side makes it easier to bring new ideas to the company ”.
BOX
Identity Card
Ceccarelli was founded in 1979 thanks to the initiative of its founder, Bernardino Ceccarelli, who in forty years has managed to make it an important industrial group, a point of reference in the transport sector first and then in logistics. Five companies gravitate around the group holding, Ceccarelli Finanziaria: Ceccarelli Srl (groupage transport), the first company founded in 1979; Transfriuli Srl founded in 1982 (partial and full load industrial transport); Dilog Toscana, a distribution platform dedicated to the Tuscany region, created in 1999 together with three other partners; the internal software house Euro's Srl, founded in 2017, which creates IT solutions related to the management of the supply chain for the group and for external customers; finally, LogLab (Logistic Laboratory), operational since 2018 through which Ceccarelli Group offers an engineering consultancy service for the simplification of supply chains. The group currently has 80 employees and 5 offices: Udine, Trieste, Padua, Milan and Prato (Dilog). The consolidated turnover in 2019 was equal to 36,120,736 Euros.
(Fonte: Ceccarelli Group)
Il Giornale della Logistica - 2021